Swagers
A cost efficient way to point, reduce & form rod, wire or tube
Metal is Formed, not Machined | No Wasteful Chips
Based on a simple principle, swaging is the process of shaping metal or forging by means of a series of very rapid blows delivered by rotating hammers, which form dies around a piece of work.
Swaging machines offer a highly cost-effective method for pointing tubing, rods, and wire for redrawing and sizing, reducing, shaping, tapering, bonding, or forming metal parts, making it a smart investment for any metalworking operation.
Swaging can be performed hot or cold, although cold is popular because it hardens most materials. The swaging process also improves grain structure, giving the part greater strength and an unusually fine finish.
Maximize Productivity with FENN Swagers
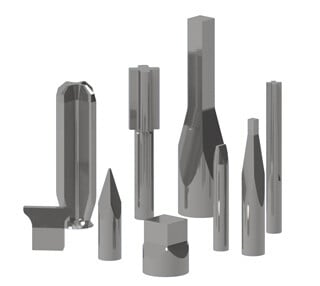
Stationary Swagers
Used for the pointing, sizing and forming of wire, rod and tube. With a rotary swaging machine, the swaged section is always circular. Rotary swaging machines include 2-die and 4-die configurations.
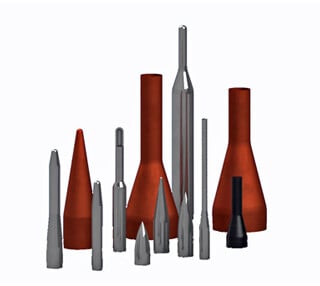
Rotary Swagers
Used for the pointing, sizing, and forming of wire, rod, and tube. With a rotary swaging machine, the swaged section is always circular.
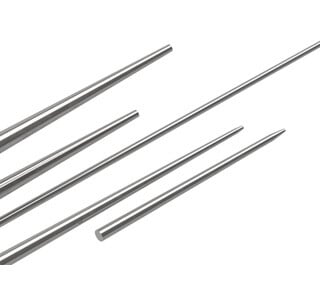
Long-Die Swagers
This type of swaging machine is only needed for taper lengths exceeding the standard die length of a rotary swager.
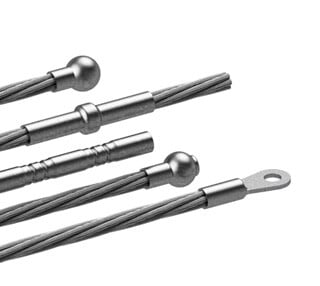
Hydroformers
Used for the assembling of parts, such as fittings to cable, and for making reductions between shoulders, such as on convoluted tubing.
Types of FENN Swagers
Stationary Swagers
Complete parts can be made from entry rounds, squares, or rectangles—hot or cold. Types include simultaneous blow used to create fluted shapes and cross-circular sections and alternate blow used to create rectangular shapes, squares, and hexagons. This method is capable of any cross-section other than a perfect circle. During stationary die swaging, the spindle assembly remains stationary, and the roller cage rotates. Shown left to right: Stationary Swagers, Alternate Blow, Simultaneous Blow.
Rotary Swagers
During rotary swaging, forming dies back by hammer blocks revolve around the workpiece. As the spindle revolves, centrifugal force throws the hammers and dies outwards against a series of rollers surrounding the spindle. Each time the hammer blocks strike diametrically opposed rolled, they are driven inward – causing the die halves to close and compress the metal being swaged. Examples include cartridge heaters, hypodermic tubing, piping, armaments, and logging industry applications.
Long-Die Swagers
This type of swaging machine is only needed with taper length exceeding the standard die length of a rotary swager. Long die swaging utilizes the same principle as the rotary method to produce long, shallow tapers for items such as furniture legs, sporting goods and aerospace products. Serves a wide variety of materials: both welded and seamless tubing of either ferrous or nonferrous metals, from stainless steel to aluminum.
Hydroformers
Hydroforming is a modification of the rotary swaging principle, where wedges are used to open the dies while the spindle is rotating so the workpiece can be inserted before and removed after swaging. It is used for assembling parts, such as fittings to cable, and for making reductions between shoulders, such as on convoluted tubing. Examples include sailing rigging equipment, architectural cable railings, and recreational ropes course cables.
Basic Swaging Applications
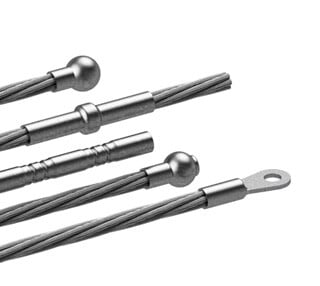
Assembling
A fitting is set over a cable, then inserted into the Swager, while the cold forming force of the hammer actions produces a completely assembled piece. Examples include: Sailing rigging equipment, architectural cable railings and recreational ropes course cables.
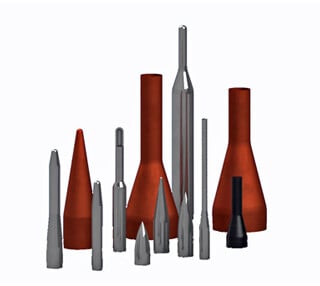
End Forming
A single piece of tube or rod is inserted into the Swager to a specified depth and reduced to a smaller diameter. The piece may be complete or ready for secondary operations such as drawing, drilling, or tapping. Examples include Aerospace tube components and fluid control tubes.
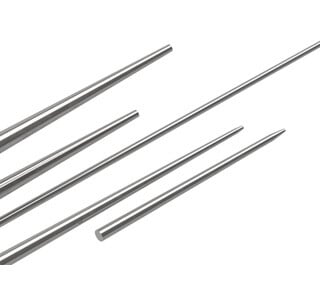
Through Swaging/Reducing
Long lengths of cable, rod or tube are passed through the Swager. The entire length of the material is reduced to a smaller overall diameter, and the cold forging process produces a desired tensile strength of material property. Examples include: Cartridge heaters and logging industry applications.
Accessories & Options for Production
Recognizing that swaging machines have many applications, FENN can provide optional equipment for your swager geared toward ease of use, process automation, and operator safety. From sound enclosures, coolant/slushing systems, and feeders to completely automated turn-key systems, FENN is ready to design and build a swaging machine tailored to your specific application. We are always excited about the opportunity to serve you and meet your unique requirements.
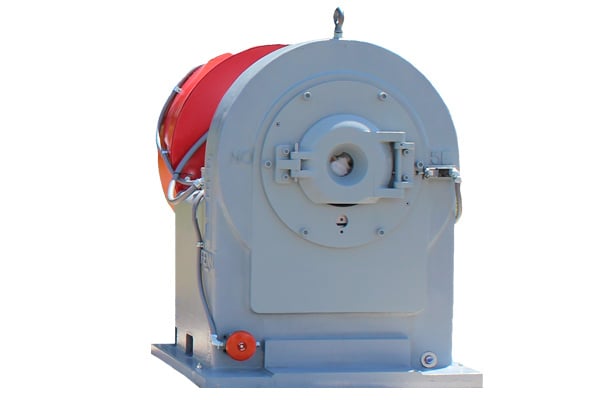
Coolant/Slushing Systems
The use of a self-contained FENN slushing/coolant system will help lubricate critical swager wear parts and keep the cage assembly free of foreign materials. Available as an option on all sized swagers.
Sound Enclosures
Reduce the sound of your swaging operation to below OSHA’s permissible exposure limit for hearing protection. FENN recommends sound enclosures for most swagers, and they provide health and safety benefits.
- Access ports can be included for features such as exhaust fans, wiring in & out, through swaging and feeder tables.
- Standard enclosures are constructed of welded 14-gauge steel, paired with 2 3/8” of soundproofing foam.
- FENN can design customized sound enclosures to meet each customer’s specific swaging requirements.
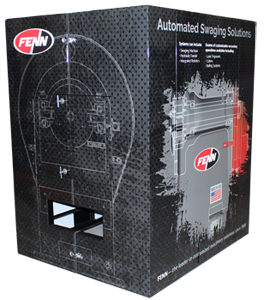
Optimize your swaging operation and increase operator safety with a Feeder
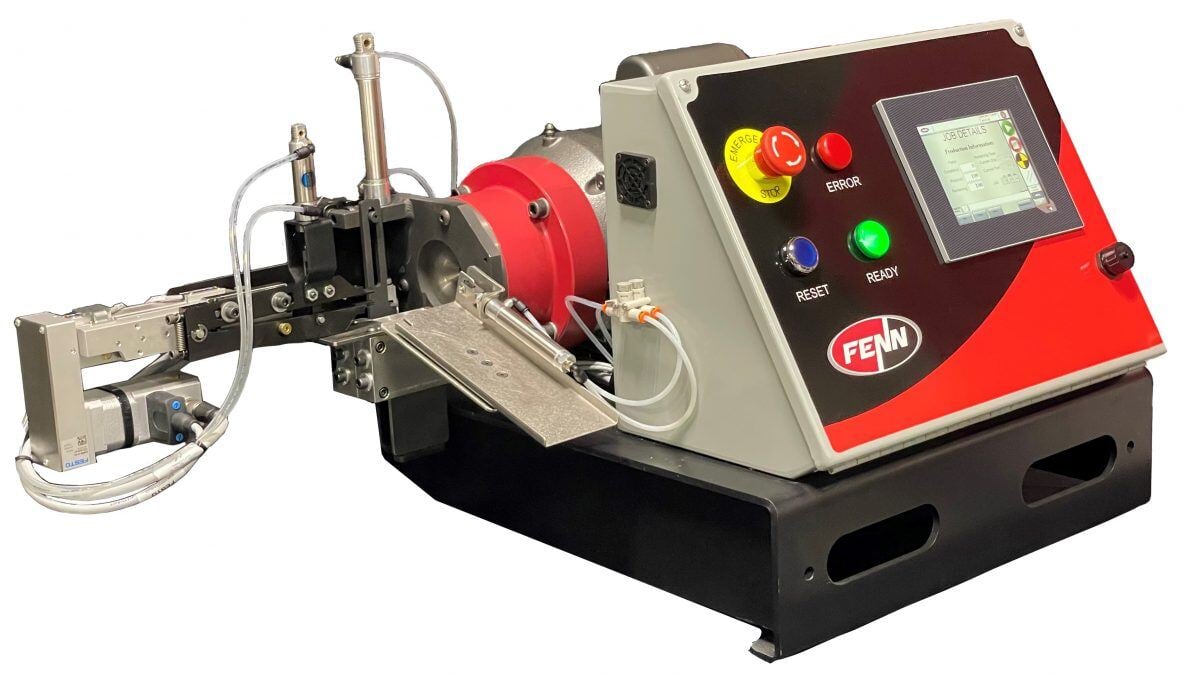
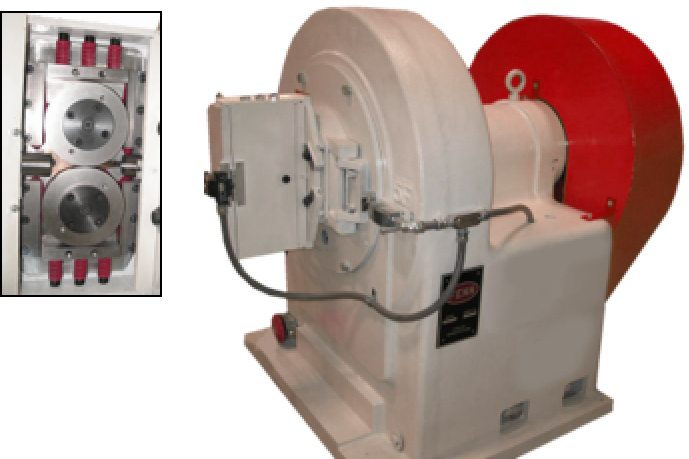
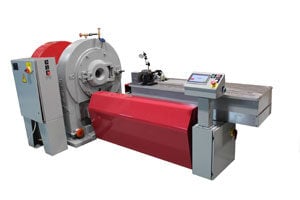
Custom Application Feeder
FENN can design a customized feeder to meet your unique and demanding production requirements. Systems are available for unique shapes, varying sizes or high capacity products. Available for all FENN swaging machines sizes NF – 8F.
Door Mounted Feeder
Mounts to the door of the swager and feeds material using hydraulically powered pinch rolls. This feed is engineered to work well with wire & rod customers to point material for drawbench use. Door mounted feeders are ideal for continuous swaging of spool material, such as high tensile wire rope. Available for FENN swager sizes 3F – 8F, others upon request. Models DM500-DM1250.
Hydraulic Table Feeder
Table feeder uses a rigid base with hydraulically powered, accurate, sliding top for precision applications. Hydraulic table feeders are ideal for high-accuracy products and high reduction applications, such as aerospace. The system is controlled using an HMI touch screen. Models 25H, 45H, 60H. Available for FENN swagers sizes 3F – 8F, others upon request.
Automated Solutions
FENN designs and fully integrates solutions to maximize efficiencies and reduce swager operating costs. In addition to designing new and customized systems, FENN can also retrofit and integrate new systems around an existing piece of FENN equipment.
- Single source supplier eliminates the need for multiple vendors to produce one system
- Automation improves equipment safety
- Collaborative robotics save time during production
- Swaging machine
- Hydraulic feeder
- Integrated robotics
- Sound enclosures
- Laser engravers
- Cutters
- Buffering systems
- Welding systems
Automated Solutions
FENN designs and fully integrates solutions to maximize efficiencies and reduce swager operating costs. In addition to designing new and customized systems, FENN can also retrofit and integrate new systems around an existing piece of FENN equipment.
-
Turn-Key Systems
- Single source supplier eliminates the need for multiple vendors to produce one system
- Automation improves equipment safety
- Collaborative robotics save time during production
-
Integrated Solutions
- Swaging machine
- Hydraulic feeder
- Integrated robotics
- Sound enclosures
-
Secondary Operations
- Laser engravers
- Cutters
- Buffering systems
- Welding systems
Swager Spares & Dies
FENN leads the metal forming industry in providing unbeatable swaging machines backed by our superior customer service, repair/rebuild program, and operator training. We also offer replacement parts, tooling, dies, and rebuild services for your machines.
Every swaging machine, die, hammer, and wear part is crafted in-house at FENN’s East Berlin, CT facility.
Our application specialists and spare parts department can help you with a full range of stock parts ready for shipment. FENN offers additional swager components and options to optimize your swaging process. Our experienced spare parts staff will help you order and receive your swaging machine spare parts as quickly as possible to maximize uptime and profitability.