Materials Research
Whether a university is using FENN rolling mills for educational purposes, a research facility is using FENN drawbenches for metallurgical development, or a client is using our swaging machines for pilot runs to improve their production process, our custom machinery has been paving the way in the materials research industry for over a century.
Another significant part of the materials research industry is performed in universities and research labs worldwide. FENN engineers are able to design and build a custom piece of metal forming machinery to perfectly fit the specifications and budgetary requirements of the materials research being performed.
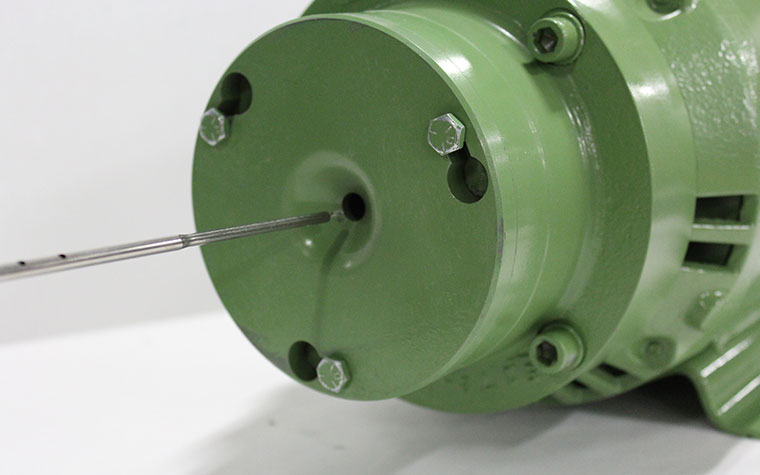
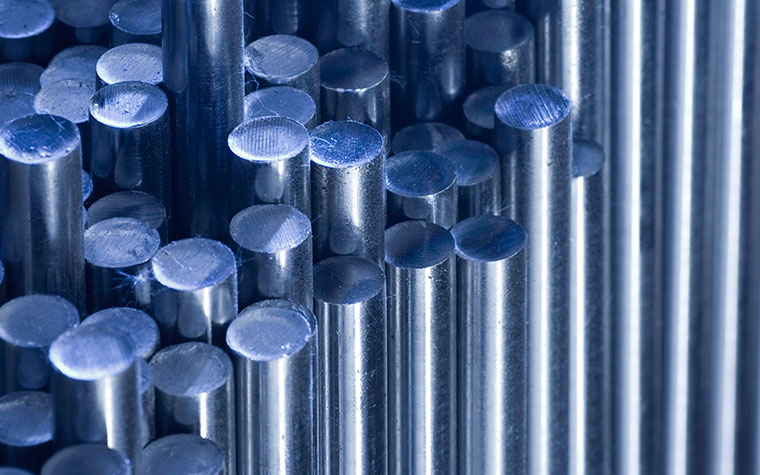
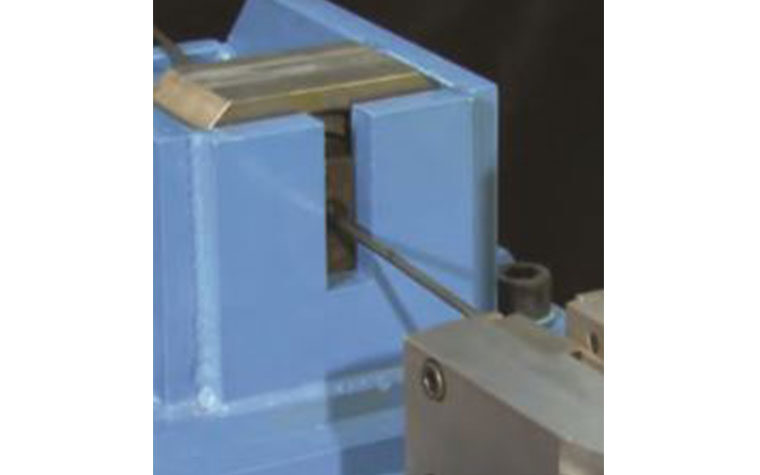
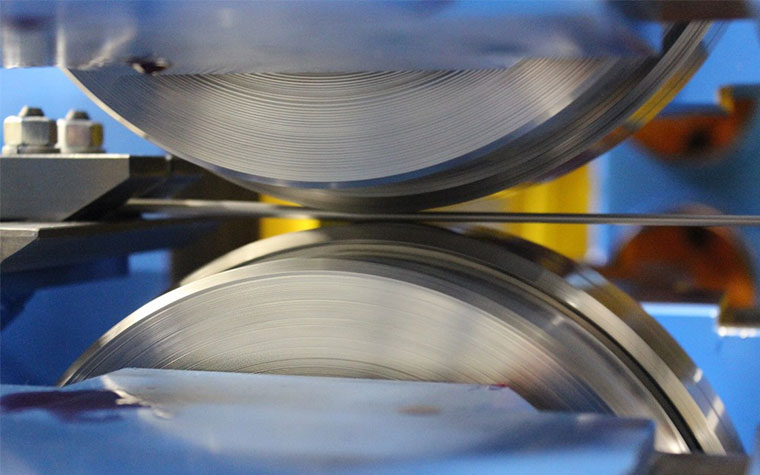
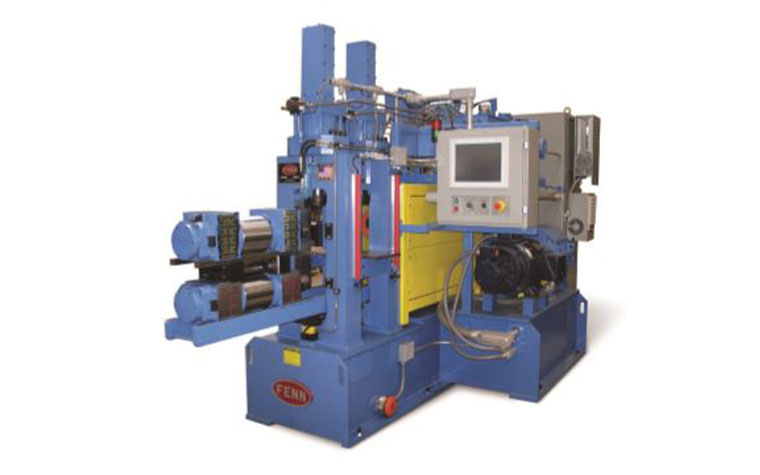
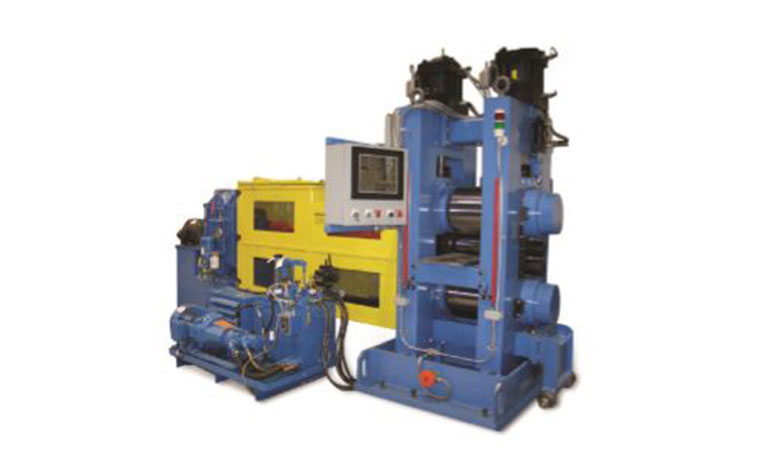
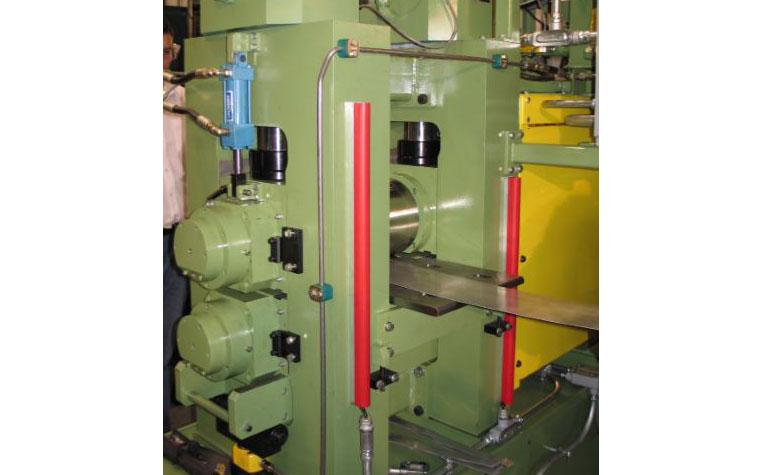
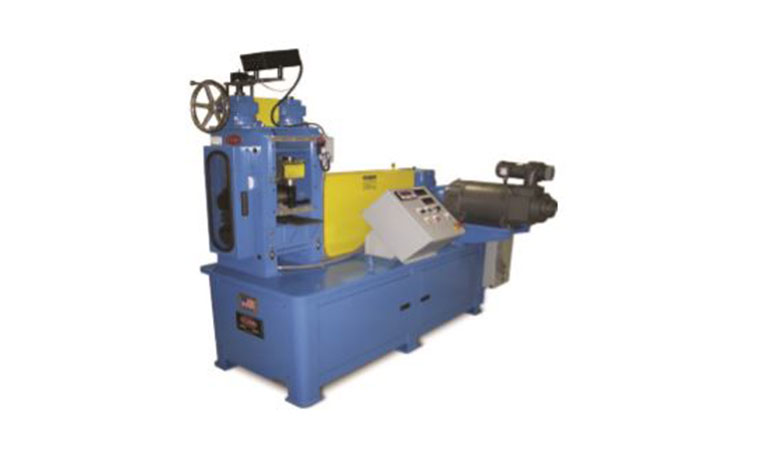
From metallurgical development in research facilities and universities to process enhancement in metal production plants, these are the most common types of FENN equipment used in the materials research industry:
- Rolling Mills – standard, custom, or laboratory mills
- Drawbenches
- Swaging Equipment
Used to roll hot or cold ferrous or non-ferrous strips, wires, and even rods, our rolling mills can be engineered to meet the unique needs of metallurgists and scientists in the materials research industry for any application up to 3.3 million lbs. (1500 MT) separating Force.
Our rolling mills can also be custom-designed to help metal producers perform test runs to refine their processes for maximum efficiency. Their advanced design, precision, incredible versatility, and reliability make them perfect for the materials research industry. Many accessory options are available for rolling mill applications.
Our full line of drawbenches is also used in the materials research industry to die-draw round rods, tubes, and wires. We offer both motorized chain units and hydraulic cylinder units to suit any research application.
FENN drawbench systems can be designed up to 230 feet long (70.1m) with 200,000 pounds of pull (90,718.474kg). A wire or tube drawing machine can be integrated to work with other FENN equipment, such as a FENN Turks Head, for producing straight lengths of shaped rod or wire.
With a vast selection of accessories, features, and customizations, FENN drawbenches bring many possibilities to clients performing materials research for educational or business purposes. Check out this video of a FENN Drawbench in action.
FENN Swagers are commonly used in the materials research industry to improve grain structure and finish. Swaging machines offer a cost-effective way to form and reshape wires, tubes, and rods. They are also effective metal-forming machines used in metallurgy laboratories to test and analyze alloy strength and grain structures.
Swaging improves grain structure since the reduction is by a succession of blows that do not seriously disturb the metal's molecular arrangement. This allows for a smooth-flowing rearrangement of grain. It is possible to swage material of a fragile crystalline structure to a point where it will become ductile enough to withstand severe bending. It has also been found that swaged pins and punches may have many times the wear life of a machine's part due to this grain refinement and increased density.
Swagers produce impressive force; duplicating a swagers performance with a slower force requires a punch press or drop hammer with massive proportions. For example, a small 1F swager weighing 625 lbs., can deliver the equivalent of 8 tons of force, a 3F weighing 1900 lbs. can deliver approximately 75 tons of force, and a 6F swager weighing about 10,000 lbs. can deliver an impressive 700 tons of force.
From metallurgical development in research facilities and universities to process enhancement in metal production plants, these are the most common types of FENN equipment used in the materials research industry:
- Rolling Mills – standard, custom, or laboratory mills
- Drawbenches
- Swaging Equipment
-
ROLLING MILLS
-
DRAWING EQUIPMENT
-
SWAGER MACHINES
Used to roll hot or cold ferrous or non-ferrous strips, wires, and even rods, our rolling mills can be engineered to meet the unique needs of metallurgists and scientists in the materials research industry for any application up to 3.3 million lbs. (1500 MT) separating Force.
Our rolling mills can also be custom-designed to help metal producers perform test runs to refine their processes for maximum efficiency. Their advanced design, precision, incredible versatility, and reliability make them perfect for the materials research industry. Many accessory options are available for rolling mill applications.
Our full line of drawbenches is also used in the materials research industry to die-draw round rods, tubes, and wires. We offer both motorized chain units and hydraulic cylinder units to suit any research application.
FENN drawbench systems can be designed up to 230 feet long (70.1m) with 200,000 pounds of pull (90,718.474kg). A wire or tube drawing machine can be integrated to work with other FENN equipment, such as a FENN Turks Head, for producing straight lengths of shaped rod or wire.
With a vast selection of accessories, features, and customizations, FENN drawbenches bring many possibilities to clients performing materials research for educational or business purposes. Check out this video of a FENN Drawbench in action.
FENN Swagers are commonly used in the materials research industry to improve grain structure and finish. Swaging machines offer a cost-effective way to form and reshape wires, tubes, and rods. They are also effective metal-forming machines used in metallurgy laboratories to test and analyze alloy strength and grain structures.
Swaging improves grain structure since the reduction is by a succession of blows that do not seriously disturb the metal's molecular arrangement. This allows for a smooth-flowing rearrangement of grain. It is possible to swage material of a fragile crystalline structure to a point where it will become ductile enough to withstand severe bending. It has also been found that swaged pins and punches may have many times the wear life of a machine's part due to this grain refinement and increased density.
Swagers produce impressive force; duplicating a swagers performance with a slower force requires a punch press or drop hammer with massive proportions. For example, a small 1F swager weighing 625 lbs., can deliver the equivalent of 8 tons of force, a 3F weighing 1900 lbs. can deliver approximately 75 tons of force, and a 6F swager weighing about 10,000 lbs. can deliver an impressive 700 tons of force.