Multi-Stand Lead Lines From FENN
Over the past century FENN has had experience designing and building customized metal forming machinery, including lead lines for a variety of industries. FENN has manufactured dozens of lead rolling lines within the last decade. Mills have been supplied for both continuous strip and cast ingot. Strip rolling is the mechanical process of reducing the gauge thickness of plate or sheet metal by passing the material through counter-rotating rolls of a rolling mill. FENN designs custom mills that are capable of rolling hot or cold material. FENN’s rolling mills have been used for a wide variety of applications such as materials research facilities and universities, rolling coins for U.S. mints, the production of cutlery, jet engine vanes, lithium for batteries, and ceramic boron to encapsulate nuclear waste.
Multi-stand lead line mill types from FENN may include:
- 4-HI Mill: A 4-HI mill may be used for finish rolling of thin gauge stock. 6-HI roll inserts are also available for narrow width ribbon and foil products.
- 2-HI Mill: Generally, a 2-HI mill is used for hot or cold breakdown and finishing of bar, sheet or strip. A wide range of sizes with separating force capacities from 10,000 lbs. (4.53 MT) to over 3,000,000 lbs. (1360 MT) are available.
- Tandem Mill: Tandem rolling mills are used to take multiple reductions in one pass, combining two or more mill stands. They are used in continuous rolling applications. Tandem mills are often used with turks heads, edgers, dancers, inter-stand tensiometers, payoff and take-up equipment.
- Mill with Winders: A mill set up with winders on either side allows for the rolling of continuous coil for sheet or thin foil.
There are many characteristics that determine the size of the multi-stand lead line and which features it will require. To begin, the maximum starting thickness of the material determines the roll diameter that will be necessary for handling the maximum reduction. The material width determines the width of the roll face, while a combination of both width and starting thickness determines the bearing and motor size of the mill. Minimum finish thickness and tolerance determines the type of screwdown and whether other features such as automatic gauge control are required. Depending upon the required reduction and application, the number of stands that are required can vary.
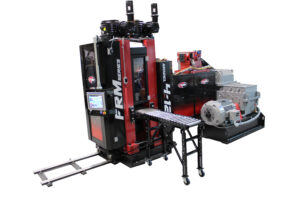
Example of a FENN Rolling Mill
Number of stands required for continuous cast lead is determined by the starting thickness and what is necessary for the final product. With the exception of the final mill stand, each mill stand can take around a 50% thickness reduction and remain within the material’s metallurgical capabilities. The final mill stand acts as a “skim pass” stand to take a light reduction.
Below is the breakdown of a typical 4-stand lead rolling line. The number of stands required will vary based on the application.
Rolling Mill Stands #1-3
- Used for taking large reductions on the material
- Mechanical handwheel screwdown to sit and hold position of the rolls
- Alternatives could be dual motor servo-screwdown, or a servo-hydraulic screwdown
- Inter-stand tensiometers on the exit side of each mill stand in order to regulate the speed and tension on the line
- Knockdown rollers between the mill stands are used to assist in automatic, hands-free material threading
Rolling Mill Stand #4
- This final stand is used as the finishing mill
- Dual motor screwdown allowing the operator to independently adjust the front and rear side of the mill to accurately produce the desired finished material thickness
Additional features of a FENN multi-stand lead line can include, but are not limited to:
- Built in roll removal rigs incorporated into the design of the multi-stand line for ease of To facilitate the changing of rolls, each stand is equipped with a built-in sliding carriage that is manually operated to remove the roll assemblies from inside the housings.
- Internal and external coolant are used to regulate the temperature of the rolls and control thermal expansion.
- External roll wipes are included to remove particulate from the rollers to maintain a clean surface finish and maximize roll life.
- Automatic gauging is used to monitor thickness on both sides of the strip in order to automatically feeds back to the finishing mill screwdown for automatic on-the-fly correction to keep the material in tolerance
FENN’s rolling mills and lines include controls customized to the customer’s requirements and preferences. An individualized software package is developed by FENN’s engineers to suit the requests of the operators. Typical controls and HMI capabilities for lead lines can include, but are not limited to:
- Displaying roll gap for each stand
- Setting the roll gap
- Setting tension values between mill stands
- Displaying current speed of each mill stand as it adjusts to balance with the speed of the lead caster
- Coolant control
- Alarms and diagnostics
FENN is proud of offer a variety of mill options to customize equipment based upon the requirements of each customer. Multi-stand lead lines can be integrated with additional pieces of equipment such as:
- Accumulators
- Shears
- Edge Trimmers for width control
- Winders
FENN multi-stand lead lines are available in a wide range of configurations and sizes, for an assortment of engineering, manufacturing, and research and development (R&D) applications. With customizations available, FENN rolling mills and shaping lines offer flexibility and numerous benefits to companies and universities who choose this equipment for their metallurgical applications. A complete offering of material handling, processing, gauging and labor-saving accessories are available for FENN multi-stand lead lines, rolling mills and laboratory rolling mills. Learn more about customized auxiliary options for FENN’s metal forming machinery.